Industry 4.0: The latest technology in refrigeration not only supports a process but a future vision of the business.
Fonderia Casati, based in Varese for a long time, has no doubts about what will be necessary to maintain its competitiveness at European level: the automation of its industrial processes, through the implementation of an integrated data flow between its production line and management control.
THE CHALLENGE
Design of the refrigeration system and monitoring of the remote parameters.
Fonderia Casati has installed a new induction furnace in its historic headquarters in viale Belforte in Varese: once again, in this case, Fonderia Casati turned to MITA Cooling Technologies to handle the cooling process, as it had already supplied the plant with a PME-E evaporative tower.
The new system’s requirements (around 400 kW, 10 °C temperature difference) were lower than the previous MITA project. In this case, however, it was necessary to supplement the cooling system with the automation of the industrial process developed in recent years by the Varese-based company.
Naturally, one objective was to take advantage of the hyper-amortization benefits, provided by the Ministry for Economic Development for the acquisition of goods and technologies that enable transformation in the direction of Industry 4.0.
SOLUTION
Open circuit Cooling tower PMS and a 4.0 refrigeration plant (industry 4.0)
We supply a refrigeration tower with a plant process or skid that supervises the refrigeration state: the collected information by the system is send to the company´s internal address, helping in the optimization of the production processes.
Fonderia Casati selected an open-circuit PMS tower, consisting of a single non-corrodible fiberglass block, suitable for small installations.
It is small in size, but with great opportunities for use: this especially if it is integrated through hydraulic connections and sensors to an automated cooling station. The MITA Systems cooling station is in fact composed of:
- a reinforced concrete tank, with a central dividing wall that allows the separation between hot and cold water; and
- a technical room for the coordination of all its typical functions using an easy-to-use touch-screen PLC.
The basic version of the cooling unit provides energy and water savings thanks to the automated regulation of a number of parameters:
- the operation, management, and control of the pumping unit and fan motor unit,
- optimization of water pressure,
- optimization of water salinity,
- checking the water level in the tanks,
- tower water treatment also thanks to the dosage of anti-scale-anticorrosive-algae additives.
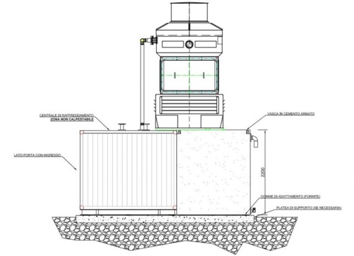
CUSTOMER BENEFITS
There is more. The customer can remotely view the parameters monitored by the Easybox cooling unit and report them to its management software: this is also required by Fonderia Casati, in its objective to be an Industry 4.0 foundry. An Ethernet connection was therefore provided between the various system components and the external data exchange over Modbus TCP communication protocol.
The entire system had low installation and maintenance costs: the components of the cooling unit are in fact pre-assembled and assembled on site using galvanized steel hardware. This facilitates disassembly even in the event of any maintenance operations.
THE COMPANY
Vision of a “4.0 foundry”
“All brands in Europe mount on its engines a piece that comes from Viale Belforte”, explains the following Italian video produced by the Unione Industriali di Varese. It also explains Fonderia Casati’s approach to Industry 4.0 as its corporate philosophy.
Since 1972 the Company has been producing castings made of special cast iron and stainless steels: turbo-compressors, turbo-manifolds, exhaust manifolds. The main customers are the European players in the automotive sector, but also the Varese brand also serves the naval sector and other general mechanical industries.
For some years now, the company has actively pursued the topic of industrial automation: Fonderia Casati manufactures its products using lines that are almost totally automated, generating a unified data flow from the plant to the company’s management. This also cuts water and energy consumption to increase the factory’s environmental friendliness.
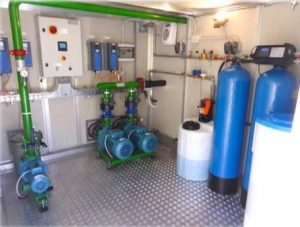